The size of the particle often determines the final properties of the product, making the particle size distribution a very important parameter for many products, such as cement, coffee, powder coatings or pharmaceuticals. In most cases, the need to measure particle size can be met by laser diffraction – a technique routinely used in laboratory and real-time monitoring for both pilot and commercial scale production. Reliable and powerful particle size measurement technology at all stages of the production cycle provides numerous opportunities for product and process improvement.
What kind of opportunity? Let us explore the application of laser diffraction particle size analysis in the coffee industry. The taste of a cup of coffee is directly influenced by the particle size distribution of the ground powder used to modulate it, so for those who grind coffee or freshly ground coffee, as well as coffee grinders or more complex fully automatic coffee machines ('bean to cup') production For business, the importance of granularity is very important.
Make the taste more perfect
Whether you are a coffee bar at a local coffee shop or a barista at a multinational coffee grinder company, your first priority is to create a delicious cup of coffee to meet your expectations. Of course, everyone's tastes are different, but there are still some obvious regional commonalities, such as the strong taste of culture in some areas, while the cultures of other regions prefer the lighter taste. Understanding the factors that influence taste is critical to the ability to successfully produce products that meet these different requirements.
The taste of brewed coffee is affected by the following factors:
â— Variety, baking method and freshness of coffee beans
â— The size of the coffee ground powder used for brewing coffee
â— The amount of coffee used per brew
â— The temperature of coffee brewing and extraction
â— brewing time / pressure
Some of these variables are dependent on the coffee producer's choice and technology, but particle size measurements are not likely to occur frequently during coffee use. Granular specifications often need to be controlled as part of the production process, such as for grinding coffee, stand-alone grinders or integrated fully automatic coffee machines.
After years of development, from the simple and well-known grinding between the fingers and the thumb, to the screening, to today's laser diffraction particle size analysis, the particle size technology applied to coffee has become increasingly sophisticated. The corresponding basic knowledge has been developed, and it is now clear that to achieve a satisfactory flavor in the brewing time that people accept, the overall particle size distribution of coffee is more important than the average particle size.
The coarse grinding coffee has a relatively small contact area, and more brewing time is required in order to release the flavor. Conversely, finely ground coffee can release flavor more quickly, but is therefore more likely to release bitter ingredients, resulting in an unpleasant, burning taste. Moreover, the very finely ground coffee tends to be tightly packed together, which can seriously hinder the passage of water during the brewing process. Therefore, fine particles generally require higher brewing pressure, and this will have an effect on the flavor of the coffee.
Coffee and coffee makers need to continue to improve their understanding of these factors in order to make coffee grinding perfect to better meet the needs of specific regions, not just for a single market. The laser diffraction method can effectively meet the laboratory's related requirements for particle size analysis, and can also provide online particle size detection for the factory production site as required.
Introduction to laser diffraction
Laser diffraction particle size measurement is a method of particle size measurement based on the detection and analysis of the resulting light scattering pattern as the laser beam passes through a particular sample. Small particles scatter light relatively weakly and have a wide angle; larger particles scatter light at an angle close to the incident beam. Using Mie's optical theory, the overall particle size distribution of the sample can be calculated based on the obtained scattering pattern without any instrument calibration.
Efficient, non-destructive laser diffraction is essentially a fast method, primarily because it is a collection-grain technique, which means that it directly measures the particle size distribution of a sample, rather than establishing a particle size measurement of different individual particles. The desired particle size distribution. Sample preparation is very simple and requires only the main requirements for proper dispersion of the sample. For coffee, the basic particle size of the sample should be the particle size of a single coffee ground powder, rather than the particle size of any agglomerate size, which is important for the behavior of coffee flavor release; therefore, the sample is efficiently dispersed during the measurement process to become coffee. A prerequisite for particle size measurement.
The laser diffraction particle size analyzer used in modern laboratories is versatile, highly automated, and extremely efficient. The latest measurement system is driven by intuitive software and can range from 0.01 to 3500 microns, enabling accurate and reliable particle size measurement even for new users. Equally important, for users of coffee particle size measurement, the system described above has an extremely powerful and efficient dry dispersion system that enables rapid and efficient measurement of viscous materials in coffee abrasive particles.
After entering the production environment, with the online system outputting the output frequency of four complete particle size distributions per second, the laser diffraction particle size measurement has obvious advantages in terms of test speed. The real-time monitoring provided by the system can greatly improve the process and automation of the grinding process, and can also be used on the production line, such as strengthening the quality control of the grinding machine (see case study below). At the same time, the instrument creates an interface between the analyst and the production line to ensure the relevance and reliability of the analysis and present the data in a way that is easy for the operator to understand and use.
The following case study contains data on how the laser diffraction method provides strong support for everything from laboratory development to the day-to-day production cycle of the plant.
Case Study 1: Comparing the particle size distribution of different varieties of coffee
Figure 1 shows the particle size distribution of three commercially available ground coffees: follicular, sleek, and concentrated roast. Particle size analysis of each sample was characterized using a Mastersizer 3000 (Malvern Instruments, UK) equipped with an Aero S dry dispersing unit. With a wide dynamic range, the instrument can successfully measure large particles inside the sample in a single measurement, while accurately quantifying extremely fine particles in the sample.
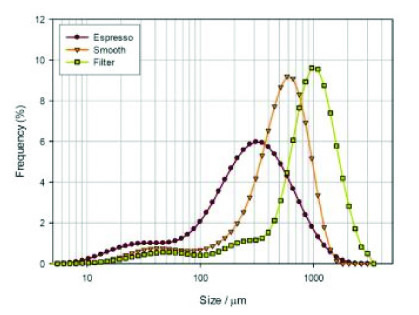
Figure 1: The particle size of espresso, scented coffee and follicular coffee highlights the effect of coffee fineness on flavor, with espresso coffee with high fines content releasing a unique bitter taste.
The results of the measurements show that the fine granules in the espresso coffee product account for a large proportion, resulting in the bitter taste characteristics of this coffee. In contrast, smooth coffee, especially follicular coffee, has a much smaller proportion of fine particles and a smoother taste. This type of laboratory analysis can be used for quality control, while also helping developers to deepen their understanding of how to optimize individual particle size distributions for a delicious understanding. This is especially important for those who work at the forefront of the industry.
Case Study 2: Optimizing Grinder Settings
The data in Figure 2 shows that once the particle size distribution of the target is determined, it can be used to support the setting of the grinding machine on the production line, ensuring that the abrasive particles from the grinding box can directly modulate the ground coffee that is satisfactory to the target customer group. . In this experiment, the measurement of the particle size can reflect the size of the grinder gap of the grinder. Lowering the setting parameters is equivalent to reducing the above gap, and it can be observed that the produced particles are finer. Laser diffraction data can effectively track the impact of the grinder gap on the particle size distribution, providing a solid basis for operating to meet specific requirements. For customers who like the bitter taste of espresso, parameter setting 1 is better, while higher parameter settings result in a smoother coffee.
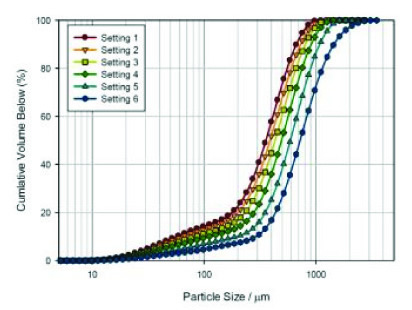
Figure 2: Increasing the setting parameters is equivalent to widening the grinder gap. As can be seen from the grinder parameter setting questionnaire, increasing the setting parameters can make the grinding particles thicker.
Case 3: Real-time grinder quality control
At the production site of Mignagola di Carbonera in Italy, De'Longhi (one of the world's leading manufacturers of coffee machines) has taken an important step to provide real-time grinding machines for fully automatic coffee machines by installing on-line laser diffraction measuring devices. Quality control. Specifically, a 100% data-quantitative quality control test is implemented within a time frame that is consistent with the dynamics of the production line. Online measurements have proven to be important in real-time monitoring of qualified/unqualified products as needed.
Figure 3 shows the status of the online particle size analyzer in the installation position, under the test bench, and when the operator views the screen. During the test, the worker on the assembly line poured fresh coffee beans into the grinder and started the test procedure. The grinder begins to work, and the resulting ground coffee flows out of the grinding chamber and flows down into the analyzer; the venturi unit then distributes the sample into the measurement area of ​​the instrument. When the ground coffee comes to the measurement area, the laser illuminates the sample and scatters, automatically triggering the measurement without human intervention. At the end of the analysis, it will be done in the same way.

Figure 3: The online particle size analyzer (Insitec, Malvern Instruments) provides real-time quality control measurements for the grinder on the production line (left). The simple measurement results directly inform the operator of the degree of adjustment of the gears, so that the grinder's work meets the specified requirements. In this case, just adjust the gear one turn (as shown on the right). ).
Despite the measurement of the particle size distribution data, the most characteristic aspect of this technology is that the way the data is presented is precisely customized according to the requirements of the test. The operator needs to focus on the green area on the screen, which shows whether the performance of the grinder meets the requirements. If it is not required, how many turns the gear is required to correct the problem. The above test guidelines are automatically generated by comparing measured particle sizes to established standards in software. After performing any corrective action, it will be tested again.
Refining the analysis to such a level of simplicity and efficiency requires some effort at the beginning, but the final solution is very successful. Although the measurement process takes only a few seconds and the number of coffee samples required is relatively small, the results produced by the measurements are very robust and representative. Because the grinder test uses a real coffee sample with a small sample size, it has the distinct advantage of reducing the ongoing cost of testing. We test each grinder and when they leave the test bench, they have a complete set of data test results that verify their performance.
In practice, today's test methods have become programmatic and very straightforward, and artificial errors are kept to a minimum. Insitec is an extremely reliable system, as evidenced by years of application in the industry. The operator cleans up the analyzer every week. This simple task takes only a few minutes; in addition, the system requires little additional maintenance. As production scales expand and new pipelines continue to be added, manufacturers are equipped with dedicated on-line particle size analyzers in each grinding area.
in conclusion
In recent decades, laser diffraction has matured and has developed into a versatile and powerful industrial particle size analysis technology. Users who explore their potential with rich imagination can get timely and powerful granularity data, which supports the various stages from initial development to daily production cycle. The above exploration of the application of laser diffraction technology to coffee particle size measurement highlights the potential advantages of this strategy and the value of those who target extremely high-end products and process performance.
Valentines Gummies,Valentine Gummy Candy,Valentine'S Day Gummies,Valentine'S Day Gummy Candy
Montreal Shantou Food Co., Ltd , https://www.montrealsnack.com